Autonomous LiDAR Drone for Tunnel Inspection: Mapping the Unknown
2021 – 2022 | near Kitimat, BC
Autonomous Drone Captures Critical Tailrace Survey Data
Inside a mountain in the Kitimat Ranges on BC’s northwest coast is a 475-metre long, 8-metre wide “tailrace” tunnel that transports the outflow water from the hydroelectric generation station in the mountain. The client, Rio Tinto, required a detailed interior survey of the tunnel for ongoing maintenance purposes and the tailrace could not be shut down for inspection. McElhanney provided bathymetric survey expertise to launch an autonomous drone mission that captured 3D scans of the tunnel interior to provide the client with the high-definition data they required for the structure.
McElhanney had to find a way to survey the interior of the tunnel without having operations shut down. Early discussion with the client included using a remote operated vehicle (ROV), autonomous surface vessel, and a floating inner tube with sensors. Eventually, an aerial solution was chosen.
This project won the 2023 Challenging Non-Cadastral Survey Project at the David Thompson Awards, hosted by the Association of Canada Lands Surveyors (ACLS).
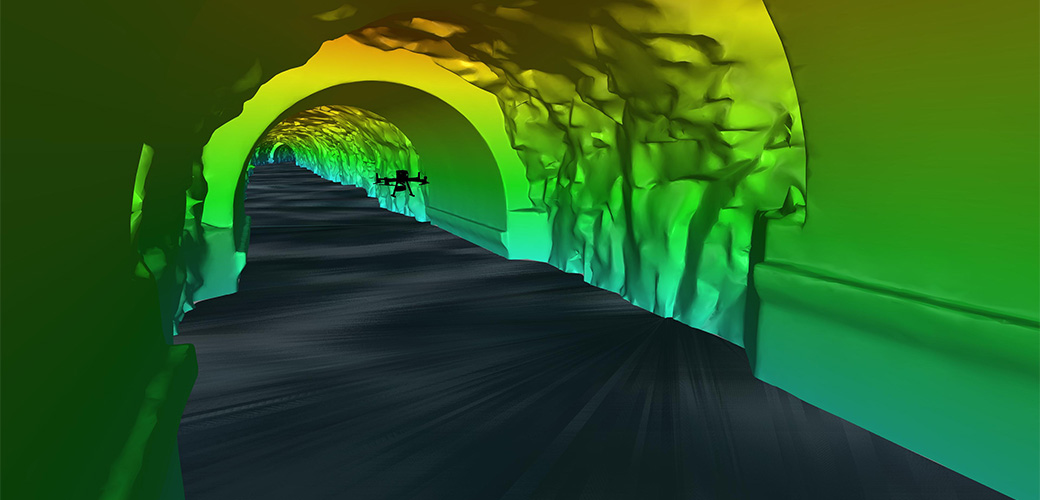
Using Autonomous Technology & 3D Scanning to Provide a Safe Mission with Low Environmental Impact
Our team led the mission planning to identify the equipment and technology needed to safely inspect the tunnel with constraints that included:
- Bended tunnel,
- A half-kilometre mission into the mountain,
- Low or zero visibility,
- GPS-denied environment (no signal transmission for operator-unit communication), and
- Water outflow velocity and turbulences.
“With the client’s support, we chose a DJI Matrice 300 unmanned aerial vehicle (UAV) with Hovermap,” said Marcell Iseli, Project Manager. “This option gave us the best chance of success to gain an interior view of the tunnel, displaying not only videos and photos but measurable spatial data as well.”
The system included a high-resolution light detection and ranging (LiDAR), video, and motion unit with an autonomous navigation system that uses simultaneous localisation and mapping (SLAM) technology. The unit was equipped with Autonomy Level 2 (AL2) software so it could fly beyond line-of-sight and communication range within the GPS-denied environment.
The team planned meticulously for the risks. The mitigation plan included retrieval nets, careful flight planning to avoid obstacles, and disabling the global navigation satellite system (GNSS) to avoid powerline interference on the approach.
Using precise control points and proprietary software, the McElhanney team created a point cloud, 3D model, and video fly-through for Rio Tinto to experience a full picture assessment of the interior.
“The client was happy that our team used this environmentally friendly and advanced technology to collect crucial data,” said Marcell.
Watch the video on the project:
Explore joining our David Thompson Award-winning team:
Learn more about:
- The Association of Canada Land Surveyors’ David Thompson Awards
Get to know more about related McElhanney services:
- Geomatics (Survey)
- GIS and Remote Sensing